Manufacturers around the globe have shifted their design processes from 2D to 3D, as it inevitably allows better design communication and assists in enhancing the production efficiency. However, there are many cases where the design data is available only in 2D, maybe only in PDFs or in sheets of paper. This happens mostly for legacy products that were designed in the pre-3D CAD era. While these products may be old, but would still be important for a manufacturer. The legacy part could be an integral component of the new product. There is also a possibility that the old design data may have been completely lost and there might be a need to improve the design of the product. But with no design data available, one may need to re-design it from scratch.
Such situations are common for many of the product manufacturers. However, the solution to this lies with the application of Reverse Engineering. With RE, it is possible to recover design information for products that have no documentation available. It is through this process that manufacturing units can convert the legacy data to editable 3D CAD formats and develop manufacturing drawings from it. This approach helps in keeping the data from being lost or damaged. In addition, Reverse Engineering can also be used to study existing product designs for any flaws or perform a competitor analysis to bring better products to the market.
Problems with Legacy Design Data
Legacy design data is old and developed years ago. There is often no known 2D drawing or 3D CAD models available, making it difficult to manufacture the product when there is a need. The issue is present even with aircraft manufacturing companies. Most of the parts of the aircraft we see today were developed years ago. It is really difficult to get design data for such aircraft components to be able to manufacture and use it in the new aircraft designs.
A similar case is with automotive manufacturers too. There are dozens of new car models being launched every single day. It is very difficult and even costly at times for the automakers to keep stocking parts of cars that are out-dated. Even if there is any data available in these cases, it will probably be in non-editable formats. This will again cause trouble to re-design the product and manufacture it on a modern CNC machine due to lack of proper manufacturing information availability.
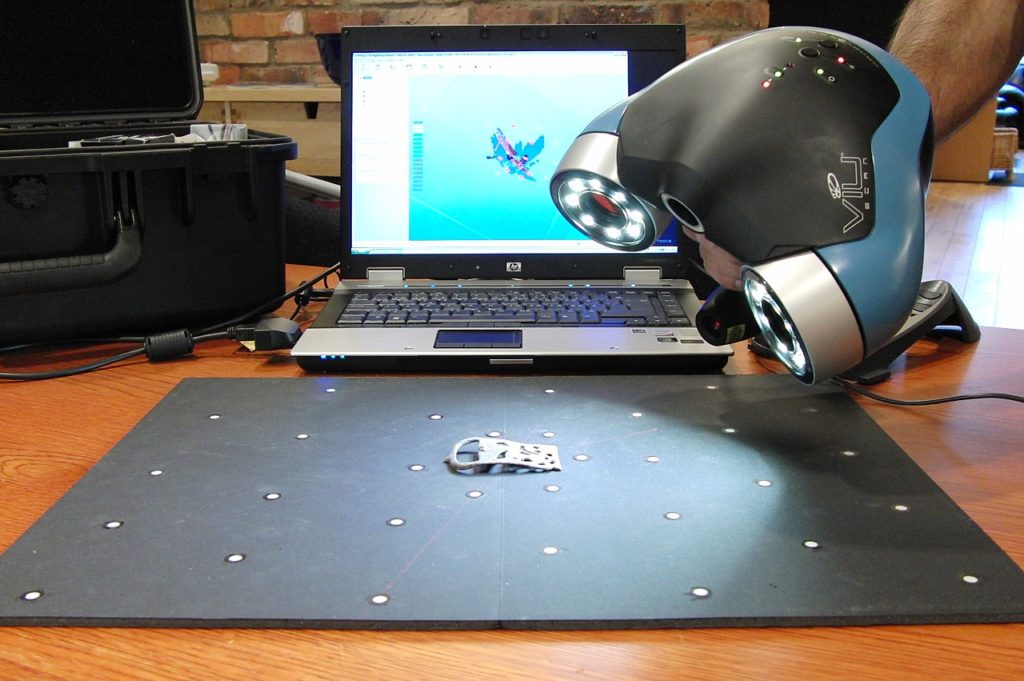
Converting the Designs to Editable 3D CAD
The process of Reverse Engineering involves scanning the part with laser scanners and/or CMM (Coordinate Measuring Machine) that capture the design data with all the features such as curves, chamfers, holes, and grooves if any in the product. This scanned or point cloud data is then verified for accuracy. Each component of the product is dismantled to be scanned to develop a digital model. A 3D CAD model is then developed to be used for manufacturing or 3D printing.
One of the vital requirements here is to maintain accuracy in the CAD model developed through the scanned data. This task is usually performed on tools like Geometric X. The tool allows performing deviation analysis, which helps the engineers to identify how accurate the scanned geometry when compared to the actual one.
Following possibilities open up with Reverse Engineering:
- The design data becomes editable which makes it possible to modify the design and produce manufacturing drawings easily.
- By scanning it is possible to determine flaws in the existing design and make changes to improve the product quality and performance.
- With 3D CAD model, it is also possible to perform virtual simulations to evaluate the design prior to manufacturing.
- Reverse Engineering also provides the opportunity to perform competitor analysis and develop a more competitive product for the market.
- The new design data serves as a digital archive which can be accessed all the time, ensuring that the data is safe from any physical damage.
Reverse Engineering is a productive way to quickly convert the legacy design data, study competitor products or improve the design of products whose data is obsolete. Manufacturers can avoid the cost of re-designing the products from scratch and the associated cost through this approach. The process of Reverse Engineering is also suitable for today’s manufacturing technologies such as CNC machining and additive manufacturing.
If you’re interested in reverse engineering services, send us your project requirements at [email protected] or fill up the inquiry form.